Achieving Operational Excellence: Best Practices in Industrial Maintenance
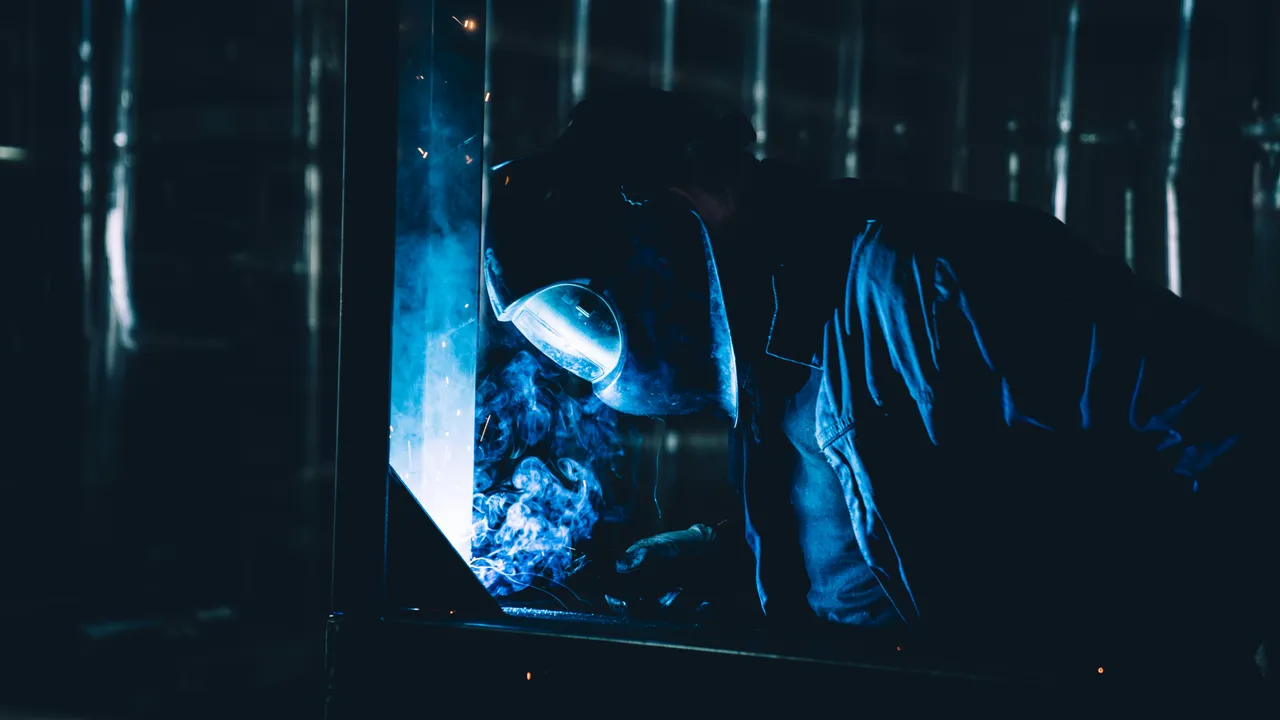
Achieving operational excellence in industrial maintenance is a critical goal for manufacturing and production facilities worldwide. This article explores best practices in industrial maintenance that pave the way for operational excellence and reliability in the industrial sector.
Importance of Preventive Maintenance
Preventive maintenance is the cornerstone of operational excellence in industrial settings. By routinely inspecting, servicing, and repairing equipment before failures occur, facilities can significantly reduce downtime and extend the life of their machinery. Implementing a robust preventive maintenance program involves scheduling regular maintenance tasks based on the manufacturer’s recommendations and historical data of equipment performance. This proactive approach not only minimizes unplanned outages but also optimizes the efficiency of maintenance operations.
Moreover, preventive maintenance allows for the early detection of potential issues, facilitating timely interventions. This, in turn, prevents minor problems from escalating into major failures that could halt production lines and lead to substantial financial losses.
Leveraging Technology in Maintenance
The integration of technology into industrial maintenance practices offers unprecedented opportunities for enhancing operational efficiency. Advanced tools such as predictive maintenance software, Internet of Things (IoT) sensors, and machine learning algorithms are revolutionizing the way maintenance is performed. Predictive maintenance, for instance, utilizes data analytics to predict equipment failures before they occur, allowing for repairs to be scheduled at the most opportune times without disrupting production processes.
These technological advancements not only improve the accuracy of maintenance activities but also significantly reduce the time and resources required to carry out repairs. As a result, companies can achieve a higher level of operational excellence through increased reliability and reduced costs.
Training and Skill Development
Ensuring that maintenance staff are well-trained and equipped with the necessary skills is essential for achieving operational excellence. Ongoing training programs that focus on the latest maintenance techniques, safety protocols, and technological tools are crucial. Such initiatives not only enhance the proficiency and efficiency of maintenance teams but also foster a culture of continuous improvement.
Empowering employees with knowledge and skills leads to better problem-solving capabilities and innovative thinking, further driving the effectiveness of maintenance operations. Additionally, involving staff in decision-making processes encourages ownership and accountability, which are key components of a successful maintenance strategy.
Continuous Improvement and Lean Practices
Adopting continuous improvement methodologies, such as lean manufacturing principles, plays a vital role in achieving operational excellence. These practices focus on minimizing waste and maximizing value in maintenance processes, thereby enhancing overall efficiency. By regularly reviewing and optimizing maintenance routines, facilities can identify inefficiencies and implement corrective measures promptly.
Lean practices also emphasize the importance of standardizing work procedures to ensure consistency and reliability in maintenance activities. This not only helps in achieving operational targets but also contributes to a safer and more organized work environment.
In conclusion, achieving operational excellence in industrial maintenance requires a comprehensive approach that combines preventive maintenance, technological advancements, skilled personnel, and continuous improvement practices. By embracing these best practices, facilities can ensure the reliability and efficiency of their operations, ultimately leading to enhanced productivity and competitiveness in the industrial sector.
This article was developed using available sources and analyses through an automated process. We strive to provide accurate information, but it might contain mistakes. If you have any feedback, we'll gladly take it into account! Learn more